There are additional applications for our nanoparticle suspensions, including capacitors and battery-capacitor hybrids, enhanced concrete performance, electrochemical sensors, and preparation of hydrophilic surfaces.
For further discussion of these applications and more detailed discussion of some of the other applications presented elsewhere on this site, visit marc-tech.com.
Adsorbents
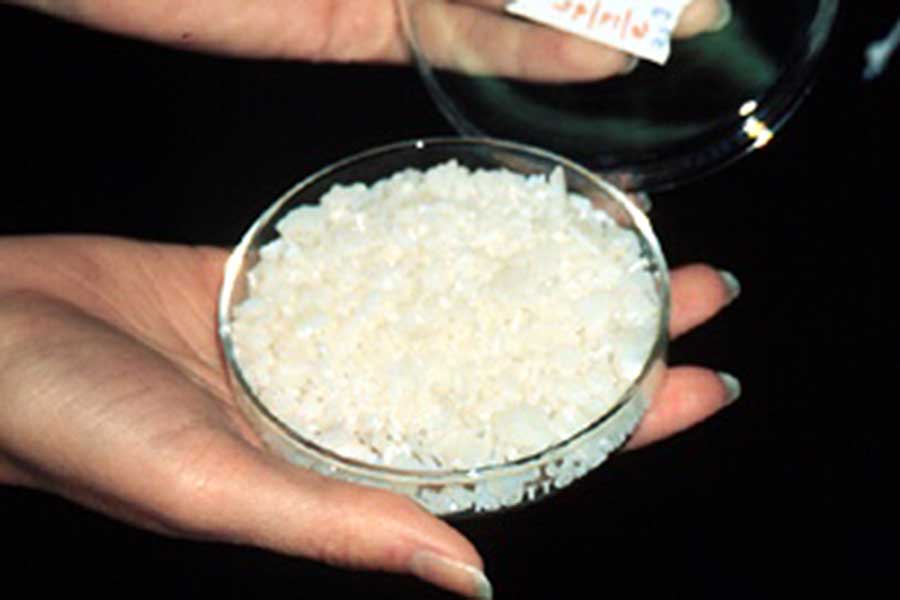
The materials offered for commercial sale by MOST are made via sol-gel processing techniques developed at the University of Wisconsin-Madison (UW-Madison). These techniques produce suspensions of nanoparticle oxides in water that are stable for up to several years. If the solvent is evaporated, the oxides will gel and form materials such as the titania particulates shown. The wide distribution of particle sizes shown in this image is typical of that occurring under controlled evaporation conditions. If evaporation is performed with strict control of temperature and humidity in a closed chamber, it is possible to obtain a porous ceramic material.
Durable Surfaces
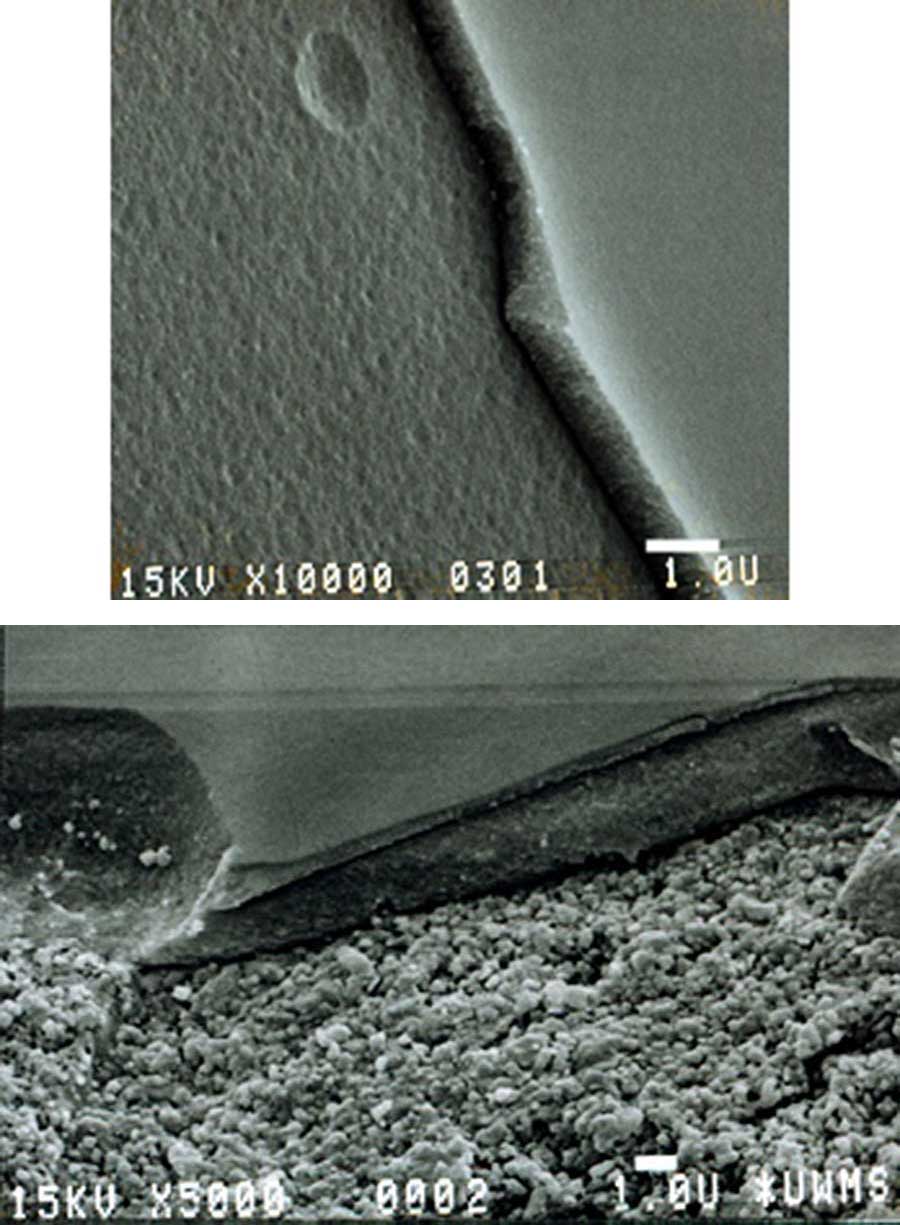
These images illustrate thin-film coatings when applied to surfaces. The thicknesses of these coatings are on the order of one micron. Coating thickness depends on several factors that can be controlled during the coating process, although these factors also depend on whether the substrate is dip coated or spray coated. MOST is capable of applying these coatings to hydrophilic and some hydrophobic surfaces (or supports).
Coatings can be applied to substrates with rough surfaces but are likely to produce a non-uniform thickness. However, as long as the substrate wets well, all parts of a substrate with a rough surface are likely to be coated to some extent.
The first two images on the Corrosion Inhibiting Coatings page show coatings applied to flat and rough surfaces.
Coatings can be applied to substrates with rough surfaces but are likely to produce a non-uniform thickness. However, as long as the substrate wets well, all parts of a substrate with a rough surface are likely to be coated to some extent.
The first two images on the Corrosion Inhibiting Coatings page show coatings applied to flat and rough surfaces.
Scratch-Resistant Surfaces
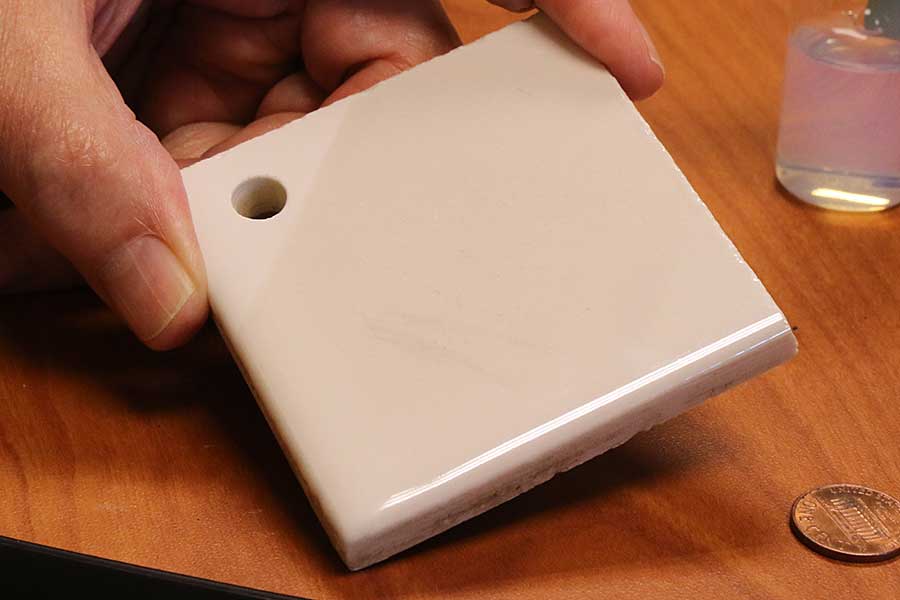
The properties of the thin-film coatings that can be produced using MOST’s nanoparticle sols depend on the temperature used to heat the coating. This image shows a ceramic wall tile that has been coated with MOST’s titania sol up to the hole in the corner of the tile and then heated to 700 C to produce a non-porous coating. The hardness of this coating has not been completely determined but is greater than 5 on the Mohs Hardness Scale.
Ceramic Membranes
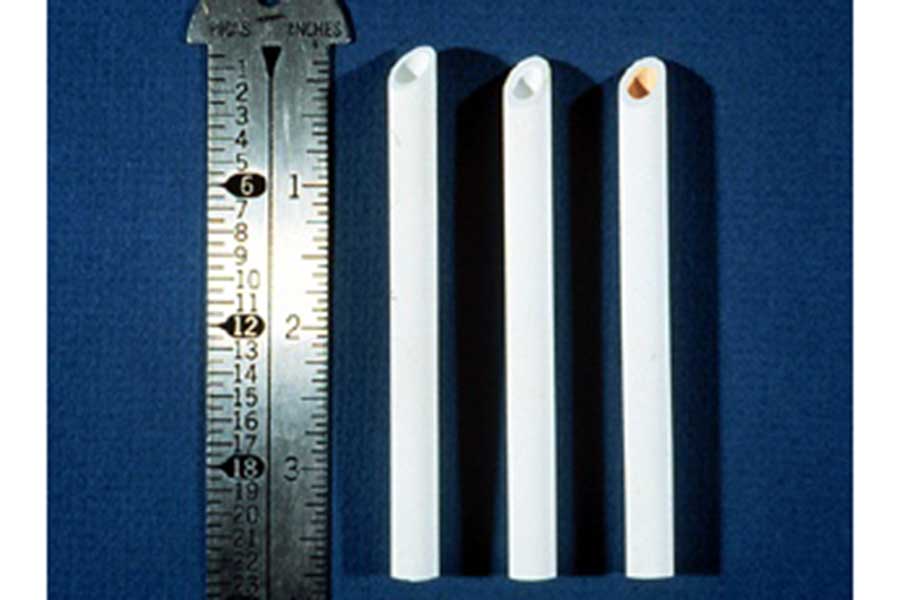
As with polymeric membranes, ceramic membranes can be used for both liquid and gas phase separations, especially at higher temperatures that polymeric membranes could not withstand. Because of the small sizes of the particles in the suspensions MOST sells (roughly 5 nm diameter or less), ceramic membranes prepared from these particles have pore sizes small enough to be able to separate small molecular weight materials if the membranes are defect-free.
The figure shows three 4-inch long ceramic separation modules. The tube on the left is a strong alumina support with a relatively large pore size. The tube in the middle is another alumina support in which a ceramic membrane with a medium pore size has been deposited. The tube on the right is an alumina support containing an intermediate pore size ceramic membrane onto which an iron oxide ceramic membrane with a small pore size has been deposited (note the reddish color on the inside of the tube). Deposition of an intermediate ceramic membrane layer is typical if the goal is to separate small molecular weight materials. (Note: MOST does not sell suspensions of iron oxide particles at this time.)
The figure shows three 4-inch long ceramic separation modules. The tube on the left is a strong alumina support with a relatively large pore size. The tube in the middle is another alumina support in which a ceramic membrane with a medium pore size has been deposited. The tube on the right is an alumina support containing an intermediate pore size ceramic membrane onto which an iron oxide ceramic membrane with a small pore size has been deposited (note the reddish color on the inside of the tube). Deposition of an intermediate ceramic membrane layer is typical if the goal is to separate small molecular weight materials. (Note: MOST does not sell suspensions of iron oxide particles at this time.)
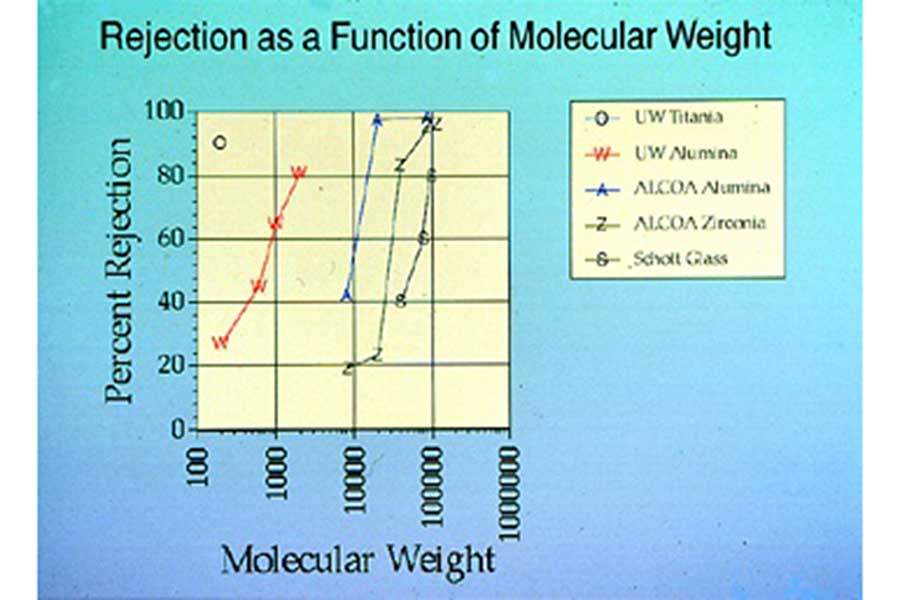
This figure shows the effectiveness of various ceramic membranes, including three commercially available ceramic membranes, at separating liquid solutions of polyethylene glycol (PEG) polymers with different molecular weights ranging from 100 to 1,000,000 grams/mole. In this figure, high values of Percent Rejection indicate that molecules of the indicated molecular weight were not able to pass through the membrane and so could be separated from the liquid in which they were dissolved. The best of the commercial ceramic membranes was only effective at separating PEG molecules with molecular weights of about 20,000 or higher. The UW-Madison ceramic membranes were much more effective at separating low molecular weight PEG molecules.
UV-Protective Coatings
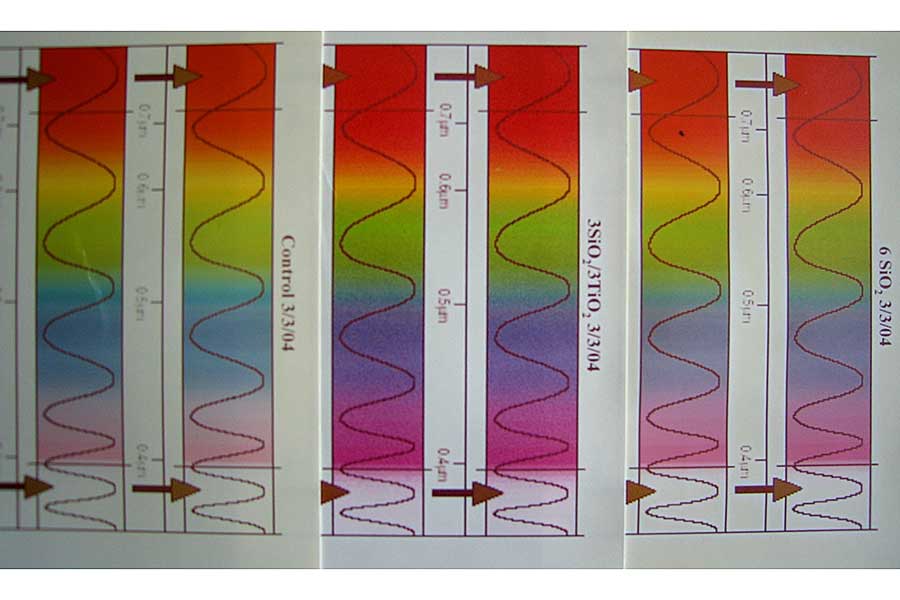
The accompanying figure shows three paper sheets printed with visible light spectra that have been exposed to a UV light source for the same length of time (click to zoom). Sheet A (far left two columns) is a control that has not been coated. The colors have clearly faded considerably when compared to the other two coated sheets. A silica coating was applied to Sheet C (far right two columns), which faded much less than the uncoated control. A silica undercoat was applied to Sheet B (middle two columns) followed by a titania overcoat, and you see the least amount of fading, retaining the most pure color.
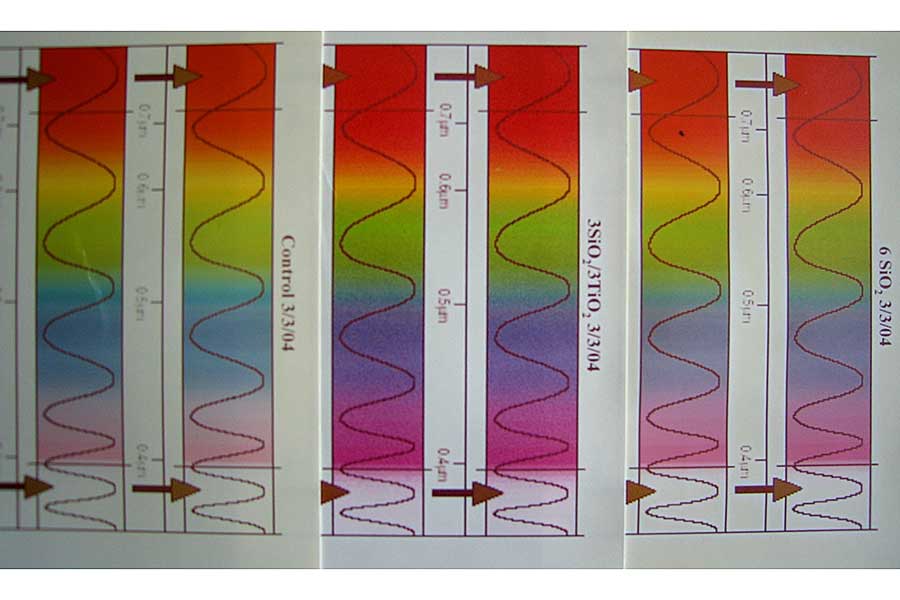
The accompanying figure shows three paper sheets printed with visible light spectra that have been exposed to a UV light source for the same length of time (click to zoom). Sheet A (far left two columns) is a control that has not been coated. The colors have clearly faded considerably when compared to the other two coated sheets. A silica coating was applied to Sheet C (far right two columns), which faded much less than the uncoated control. A silica undercoat was applied to Sheet B (middle two columns) followed by a titania overcoat, and you see the least amount of fading, retaining the most pure color.