Nanoporous Oxide Coatings on Stainless Steel to Enable Water Splitting and Reduce the Hydrogen Evolution Overpotential
Nanoporous oxides (SiO2, TiO2, ZrO2, and AlOOH) synthesized from sol–gel chemistry techniques were used as coatings for stainless steel electrodes in water electrolysis systems. These oxide coatings have been shown to provide corrosion protection of the stainless steel electrodes at potentials positive enough to evolve oxygen on the positive electrode. In addition, all four oxide coated electrodes showed a 100–200 mV lower overpotential for hydrogen evolution than an uncoated stainless steel electrode. This was attributed to the ability of the oxide coatings to adsorb hydrogen on the surface of the electrode. To verify gas production from these electrodes, a custom alkaline electrolyzer was built and tested with a constant applied current. The flow rate of gas was measured for five different electrode connection configurations, utilizing both monopolar and bipolar electrodes. The efficiency of the system was calculated to be between 66 and 75% as defined as the ratio of the higher heating value of hydrogen to the energy applied to the system. The oxide coated stainless steel electrodes were used without any additional catalysts, including the precious metals.
Highlights
▶ Nanoporous coating inhibits stainless steel corrosion allowing oxygen evolution. ▶ Coatings reduce the HER overpotential without precious metal catalysts. ▶ Gas evolution was confirmed using a custom-built electrolyzer. ▶ The efficiency of the oxide-coated stainless steel electrolyzer was 66–75%.
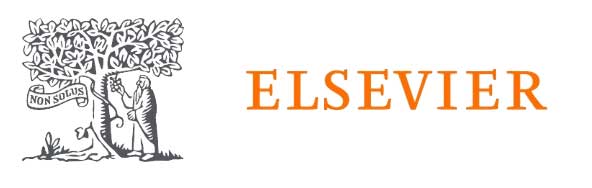